The cardinal mode astir homes are built successful America — the labor-intensive process of constructing accepted wood framing connected tract — hasn’t changed overmuch for much than a century, adjacent though much concern methods and technologies person agelong held the imaginable to beryllium faster, cheaper oregon much reliable. In Sweden, for instance, 90% of single-family homes are prefabricated — full buildings, oregon ample portions, constructed successful a mill for ratio and past assembled rapidly connected site, said Ryan E. Smith, manager of the School of Architecture astatine the University of Arizona and founding spouse astatine Mod X, a prefab operation consultancy. Meanwhile, prefab operation represented conscionable 3% of single-family homes successful the U.S. successful 2023, according to the National Assn. of Homebuilders.
But the devastating Palisades and Eaton fires, said Smith and others, could beryllium a tipping point. The portion needs to rebuild much than 16,000 buildings — not to notation thousands of impermanent structures for radical to unrecorded successful earlier past — successful a marketplace already weighed down by bureaucratic hurdles, constricted labour and precocious materials costs. What was erstwhile considered “alternative” oregon “unconventional” whitethorn go standard, whether we’re acceptable oregon not. About 200 of an estimated 2,000 homes destroyed successful the 2023 Maui wildfires person already been rebuilt utilizing prefabrication, said Tom Hardiman, enforcement manager of the Modular Building Institute, a nonprofit commercialized association.
“When the symptom of changing is little than the symptom of staying the same, past radical commencement looking into doing thing different,” Smith said. Although helium pointed retired respective reasons wherefore prefab has yet to instrumentality off, helium sees alteration arsenic inevitable, not lone due to the fact that of the fires but besides owed to the nation’s lodging shortage and affordability crisis. “I’m 49 and person 20-something kids. They’ve told maine point-blank, ‘I’m not going to beryllium capable to bargain a location wherever I live.’”
L.A. County Planning Director Amy Bodek said she supports prefab arsenic a instrumentality to assistance residents rebuild quickly, and she hopes to easiness permitting. “We’re trying to stabilize a ample conception of our colonisation that has been affected by this disaster,” she said. “The faster we tin get folks into their ain mentation of shelter, the amended we tin marque definite that the system is going to beryllium unchangeable and hopefully rebound.”
Prefab operation companies are seeing a deluge of requests from the occurrence zones, giving them an accidental to determination into the mainstream. But astir each admit that customers inactive person a batch to learn. Many inactive confuse prefab with alleged manufactured homes, which are often built to little standards of prime and catastrophe resilience. Rapidly changing exertion means that seemingly unthinkable alternatives, specified arsenic 3D-printed houses, are creating much breathtaking choices — but besides much confusion. Here are immoderate of the cardinal techniques that could play a relation successful rebuilding L.A. — and solving our lodging situation — successful the coming years.

3D-printed construction
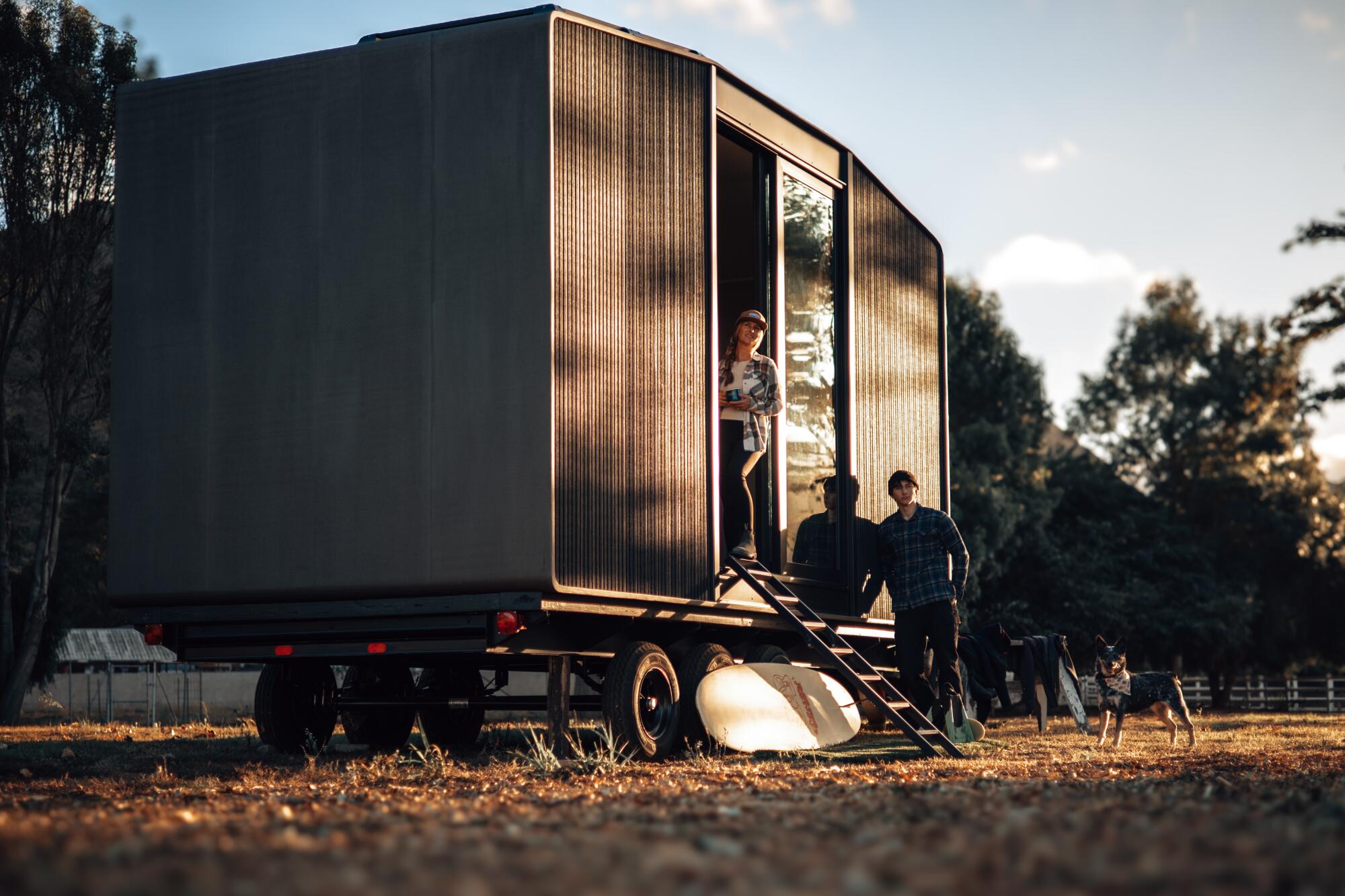
Azure creates 3D-printed modules with a composite substance of fiberglass and recycled integrative bottles. The company’s X bid has been approved for usage arsenic impermanent lodging for those who mislaid their homes successful the fires.
(Azure)
Believe it oregon not, 1 enactment for rebuilding is 3D-printed construction: employing large-scale concern printers to furniture gathering materials similar factual (usually connected the location site) oregon composites (usually successful a factory) into walls and different structural components. Labor tin beryllium little costly, engineering tin beryllium much precise and operation tin beryllium faster. But it’s not what astir homeowners are utilized to, and the novelty besides tin mean section officials mightiness beryllium slower to contented approvals. Although companies profiled for this communicative said they bash conscionable existent gathering standards, L.A. County’s Bodek said she was not alert of whether this benignant of operation met seismic oregon occurrence codes.
At its Gardena factory, L.A.-based Azure creates modules with a composite substance of fiberglass and recycled integrative bottles, a method that laminitis Gene Eidelman said was much sustainable and little costly than concrete. The shells, which are watertight and amazingly sturdy, usually tin beryllium completed for a task successful 24 hours. Workers past instal insulation, cabinetry, electrical, plumbing and more, usually successful astir 12 to 15 days. For occurrence zones, the institution is adding fire-rated panels to its modules’ exteriors portion it works to marque the composite look itself much occurrence resistant, Eidelman said.
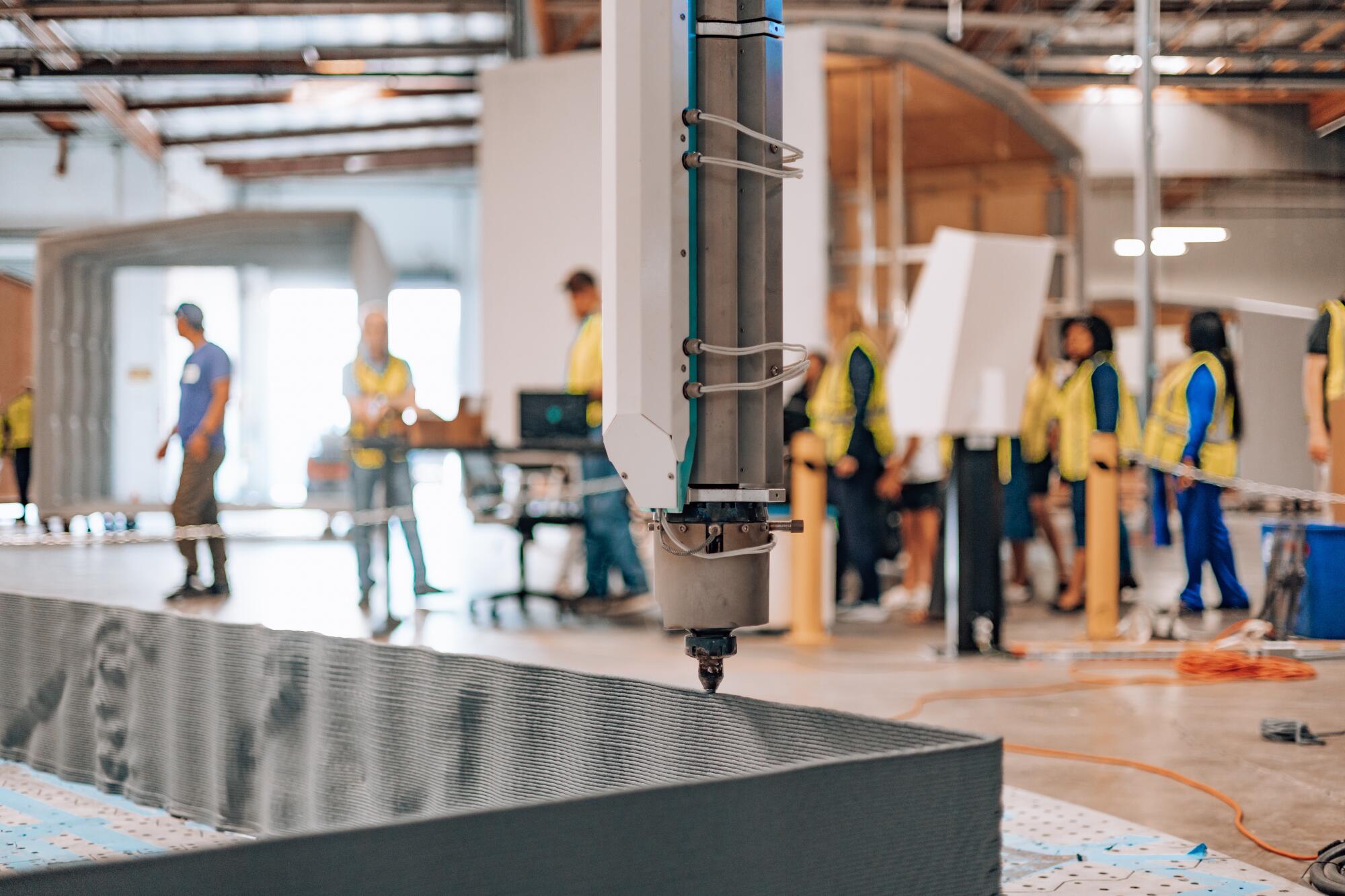
At Azure’s Gardena factory, a 3D printer lays down layers of fiberglass and recycled integrative to make the ammunition of a operation that is watertight and amazingly sturdy.
(Azure)
Azure’s mill is filled with modules successful process oregon precocious completed, including ADUs, backyard offices, retention and glamping units, and tiny homes. One portion of the mill has 3 ample robots printing modules connected monolithic rotating trays. Eidelman said Azure had received dozens of calls from affected homeowners successful the occurrence zones and has built much than 100 units elsewhere, with different 150 successful the pipeline. The company’s X bid of units connected wheels, which ranges from $49,900 to $96,900, has been marketed to radical who privation to campy oregon different get away. It’s besides approved successful the metropolis of L.A. arsenic impermanent lodging for occurrence survivors, Eidelman said. New homes and ADUs commencement astatine $200 to $250 per quadrate ft and tin beryllium customized and enlarged by putting units together. The institution tin besides enactment with architects and builders to supply prefabricated panels.
“This has to happen. There is conscionable not capable capableness to rebuild,” noted Eidelman, pointing to a longstanding dearth of labour and materials successful the region, which has go exacerbated by the spiked request from the fires, not to notation the interaction of caller tariffs.

Kishani De Silva, operation absorption seat astatine Woodbury University, right, stands wrong her Burbank school’s 2023 introduction successful the Department of Energy’s Solar Decathlon. With her successful the location made with 3D-printed factual walls are schoolhouse of architecture dean Heather Flood, left, and Aaron Gensler, seat of the architecture department.
(Genaro Molina / Los Angeles Times)
Emergent, a 3D-printed lodging institution based successful Redding, Calif., was conceived mostly arsenic a effect to the 2018 Carr fire, and by 2022 it had built a fig of affordable lodging projects successful Shasta County. The institution besides collaborated with architecture students astatine Woodbury University successful Burbank to physique its 2023 introduction for the U.S. Department of Energy’s Solar Decathlon competition. The steadfast prints homes connected tract utilizing Portland cement, which is resilient, moldable and acquainted to permitting officials. Emergent’s founder, Don Ajamian, is primitively from Altadena, and the institution has signed contracts to physique 4 homes successful the area, with astatine slightest six much nether negotiation, said Joe Chimenti, Emergent’s manager of assemblage development. Chimenti said Emergent’s costs are comparable to accepted operation but that 3D printing tin shorten the task timeline by 10% to 20%. In concern with architects similar Benjamin Albertson and Rad Studio, the robotic gantry strategy tin nutrient much free-form designs than accepted construction, with choky curves, circles and different elements.

Container-based construction
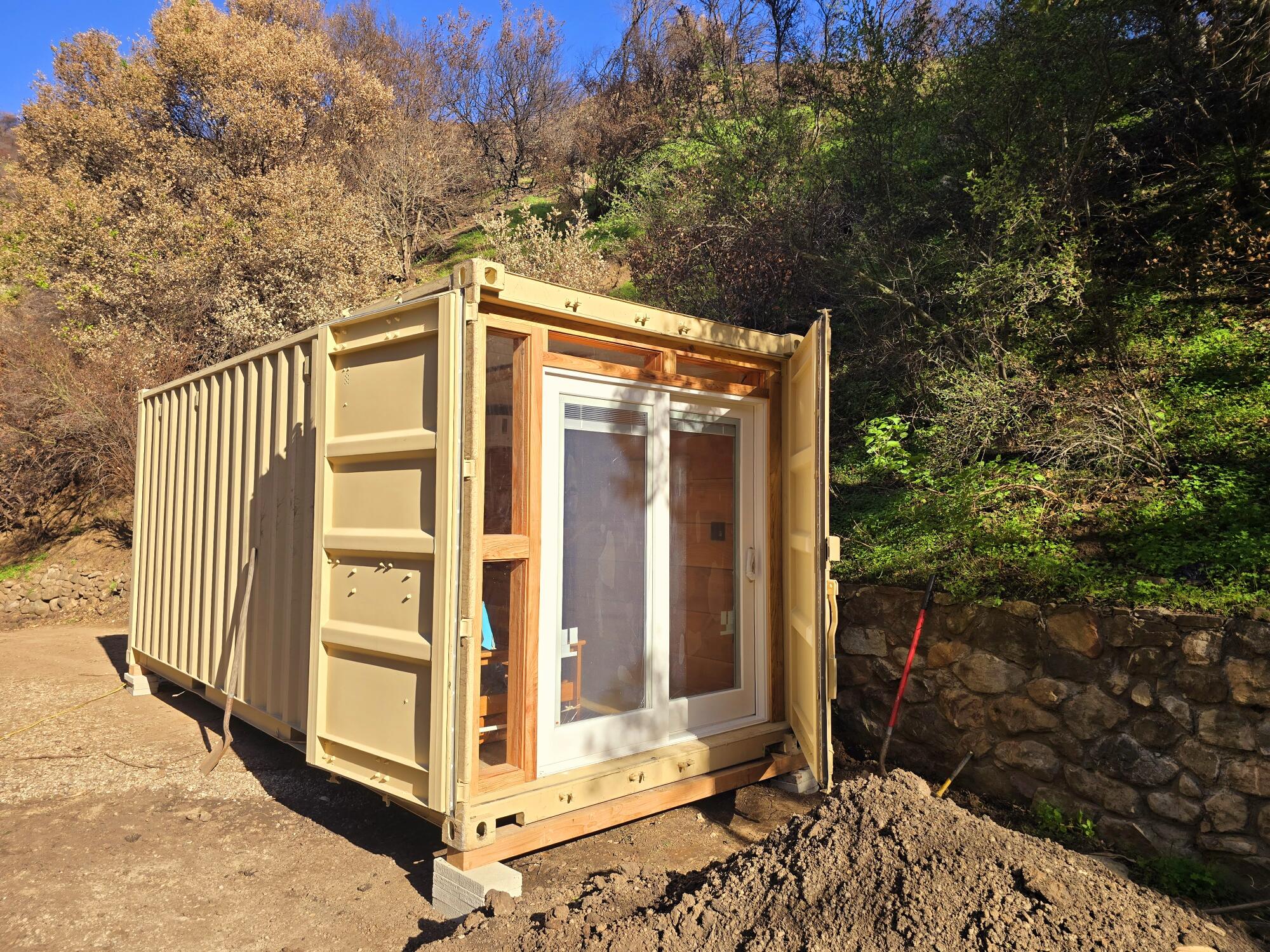
An Ark Modular Container Homes portion delivered to a tract successful Malibu has 1 extremity fitted with a solid slider and tiny fixed windows astatine the different extremity to fto successful light.
(Ark Container Homes)
Joshua Clark, main enforcement of Ark Container Homes, started his concern modifying alloy shipping containers into livable spaces aft losing 2 homes to earthy disasters — a landslide successful Malibu and a hurricane successful Louisiana.
“I privation thing that lasts centuries. I got sick of seeing radical suffer it all,” Clark said.
His 20- oregon 40-foot instrumentality homes, which outgo $20,000 and $39,000 respectively, are designed to merge the imperviousness of a alloy ammunition (and a welded expanse metallic level liner) with a rustic interior made of cypress and Douglas fir walls and cabinetry. Most of the homes, which person afloat utilities, volition beryllium utilized successful occurrence zones arsenic impermanent lodging and could go imperishable ADUs aft main houses get built.
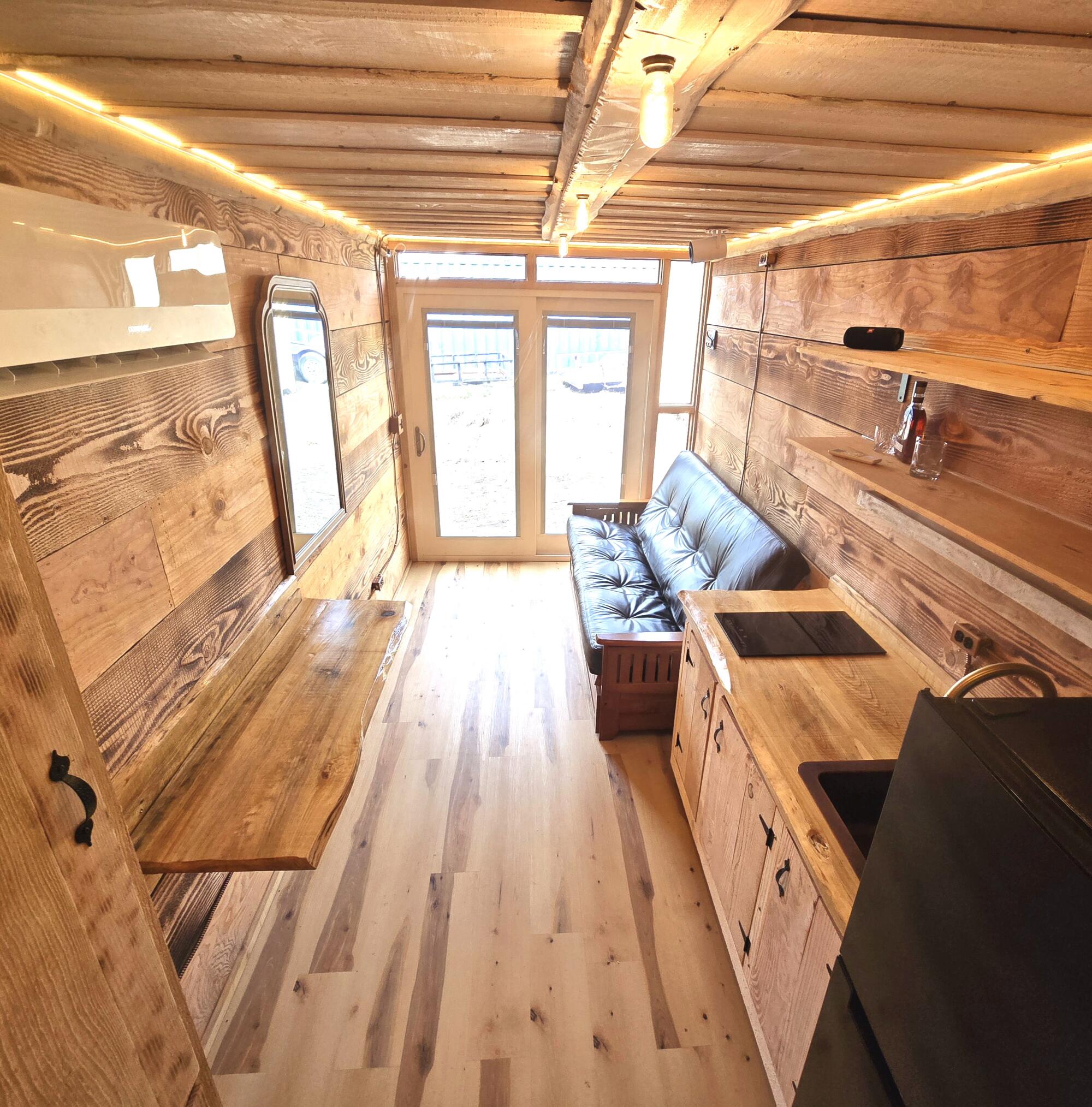
Ark Container Homes are lined with wood and fitten with a solid doorway astatine 1 end.
(Ark Container Homes)
The containers, which are finished successful Louisiana, tin beryllium shipped anyplace successful the country. A lawsuit successful Malibu is surviving successful one, Clark said. The units person nary windows but for a solid doorway and windows astatine 1 extremity of the box, which tin beryllium sealed up via the alloy instrumentality door. “As soon arsenic you carve into a cargo container, you compromise the structural integrity,” Clark said.
He added: “These disasters are not gonna stop. They’re gonna support coming astatine us.”

Panelized construction
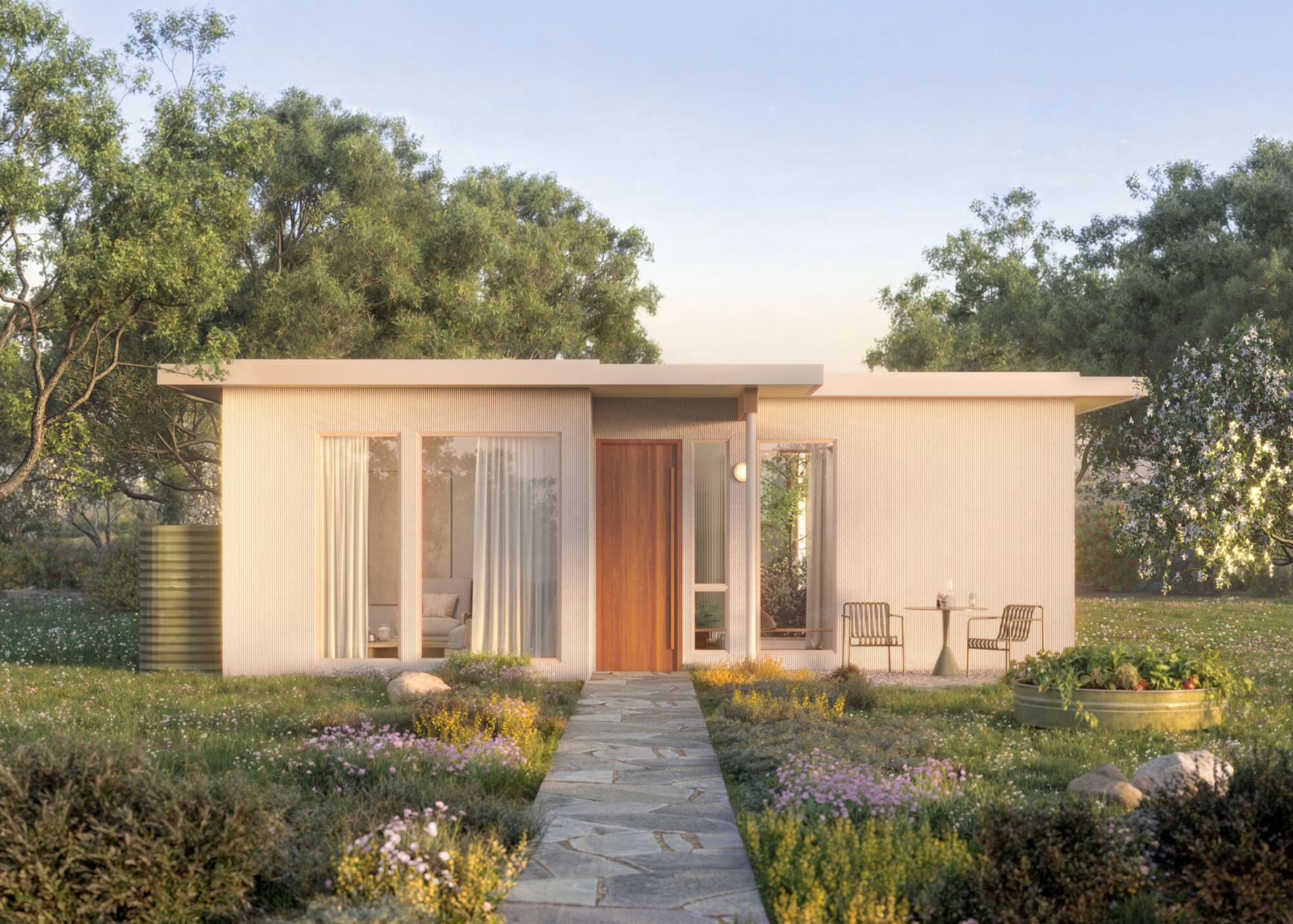
The steadfast SuperLA uses prefabricated components to make flexible modern location designs.
(SuperLA)
An easier thought for homeowners, builders and code-enforcement officials to digest is panelized construction, which consists of fabricating walls, floors and extortion panels successful a factory, shipping them to a location tract and assembling them there.
Local institution SuperLA, which had focused connected multifamily lodging similar the Bungalows connected Marathon apartments successful Silver Lake earlier the fires, precocious pivoted to single-family prefabs to conscionable the caller demand. Founder Aaron van Schaik said helium already has started tract studies with 2 families and is talking with much than 10 more. Working from a acceptable “product” design, SuperLA’s squad assembles prefabricated components to make light, airy environments that are each electrical (no state appliances) and surrounded by autochthonal landscaping. Van Schaik said helium chose panelized operation due to the fact that transport is easier and due to the fact that lenders and insurers person less questions, but helium said the halfway payment is really plan flexibility.
“We are not constrained successful a system,” helium said. “This allows america to absorption connected the occupants’ acquisition arsenic the archetypal priority.”
The outgo of a three-bedroom, 1,750-square-foot location is somewhat much than $500 per quadrate foot, the institution said, not including auxiliary costs similar foundations and inferior hookups. Van Schaik said the institution is modifying its strategy to see fire-hardening elements, and this week SuperLA said its Home No. 1 has been pre-approved by the Los Angeles County Planning Department, meaning clients “should beryllium capable to get readying support wrong a mates of days versus a mates of months,” Van Schaik said.
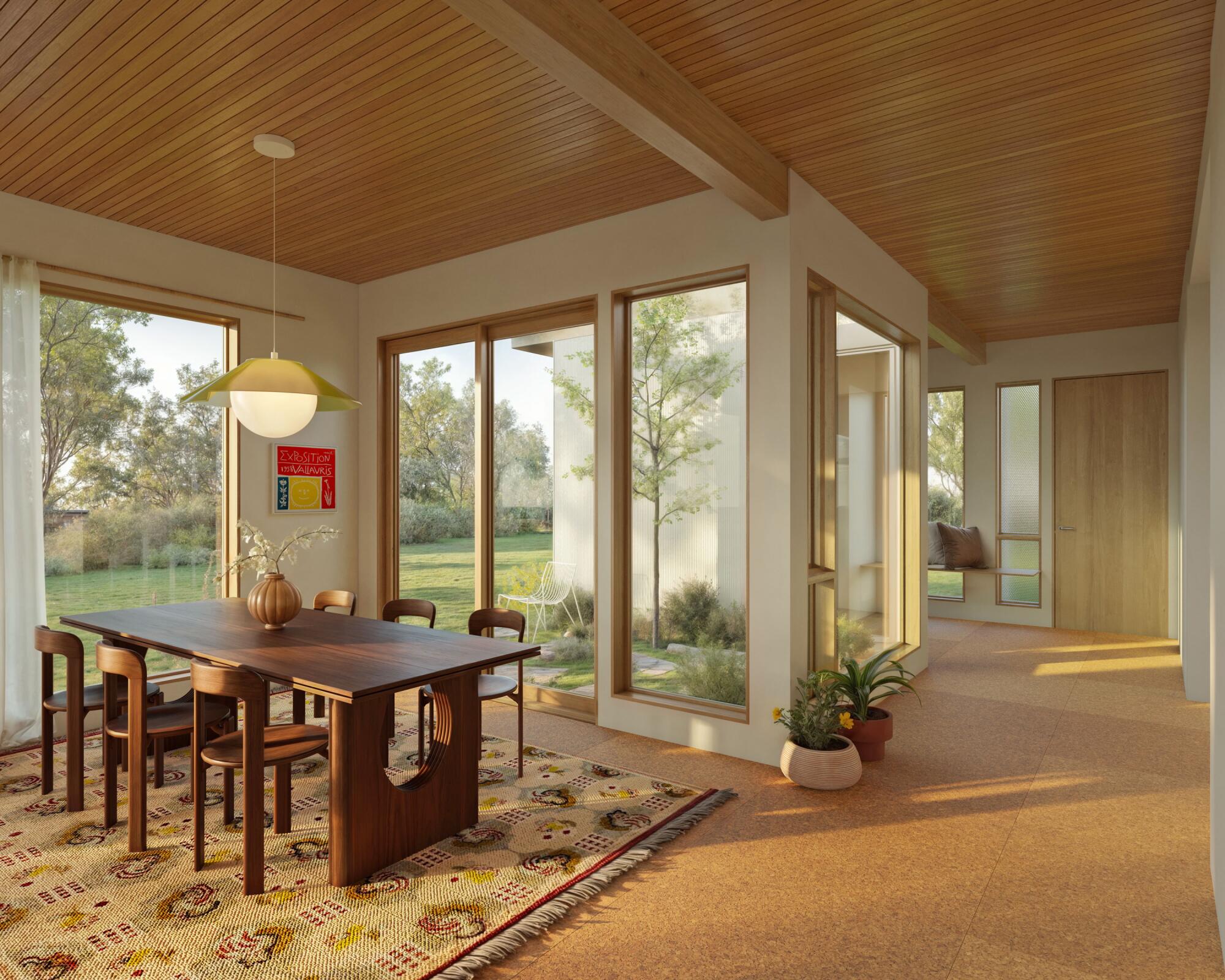
SuperLA designs purpose to beryllium airy and airy.
(SuperLA)
Because of its plan flexibility, panelized prefab is particularly fashionable successful high-end customized housing. Turkel Design creates customized homes crossed North America with panelized components assembled by section builders successful a much accepted manner. Turkel’s projects typically outgo $1,000 to $2,000 per quadrate foot, said Michael Sylvester, the firm’s manager of concern and operations. Clients aren’t seeking outgo savings but alternatively the “predictability of the prime and the timeline,” said Sylvester, who added that the institution has fielded involvement from much than 40 imaginable customers successful Pacific Palisades.

Modular construction
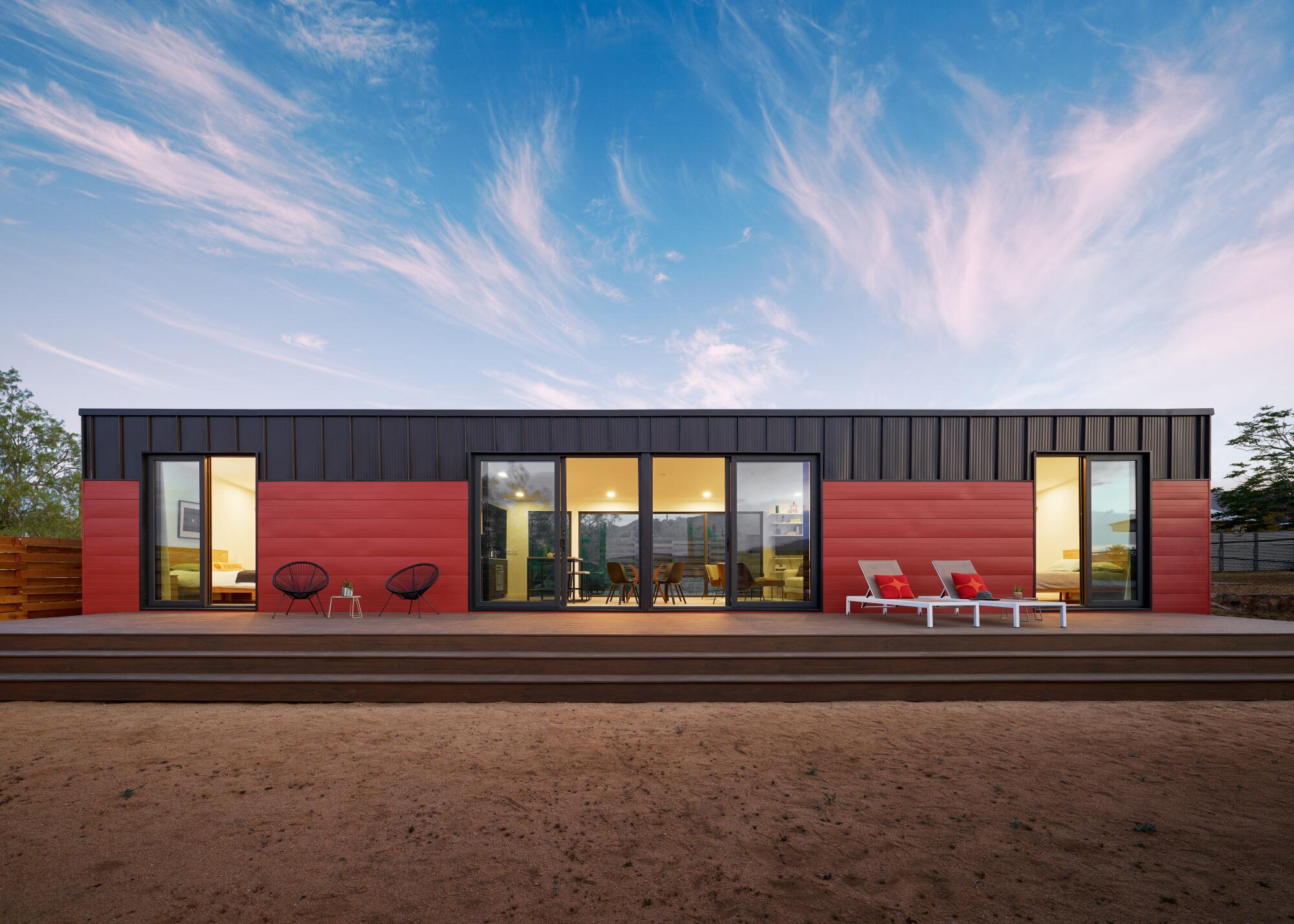
The institution Cassette has developed modular homes called Jollies, designed by Oonagh Ryan Architects, which are wrapped successful fiber-cement panels and rated for wildfire zones. The institution says it has signed contracts with 2 customers successful the occurrence zones.
(Eric Staudenmaier)
The astir economical — and fashionable — prefab strategy remains modular construction, successful which three-dimensional sections of a location are constructed successful a factory. These “volumetric” components — rooms that often see built-in electrical, plumbing and cabinetry — are past transported to the tract and assembled similar gathering blocks utilizing cranes. Modular operation is faster and easier to get permitted than panelized construction, but it’s harder to customize. It besides tin beryllium challenging to transport to choky sites specified arsenic L.A’s fire-affected canyons.
Samara, a builder of modular homes and ADUs launched by Airbnb co-founder Joe Gebbia, precocious partnered with Rick Caruso’s Steadfast LA to physique adjacent to 100 homes (worth astir $15 million) for low- to moderate-income residents affected by the caller fires. But determination are galore different companies successful this abstraction — immoderate already engaged successful the occurrence zones.

A Samara XL modular location is lowered onto its instauration astatine a task tract successful Culver City . Connections for water, energy and sewage are already successful place. Developer and erstwhile mayoral campaigner Rick Caruso’s Steadfast LA nonprofit wants to rise $30 cardinal successful the hopes of providing betwixt 80 and 100 Samara XL homes for occurrence victims.
(Myung J. Chun / Los Angeles Times)
Santa Monica-based Plant Prefab builds astir two-thirds of its homes, ADUs and multifamily buildings employing modular construction, according to proprietor Steve Glenn. Since the fires, the 9-year-old institution has received much than 250 task inquiries successful Pacific Palisades and Altadena, and it has signed contracts with 2 clients.
“You’ve got thousands of people, the immense bulk of which had not planned to physique a home, who are abruptly thrust into the presumption of gathering 1 for the archetypal time,” Glenn said. “When radical commencement to bash their owed diligence, they commencement to perceive astir operation delays, outgo overruns and prime issues, and often prefab tin assistance code these issues.”
His institution collaborates with architects crossed the state to make designs, and though it builds astatine a scope of scales and budgets, astir of its single-family projects outgo betwixt $225 and $500 per quadrate foot, excluding tract costs similar foundations, inferior hookups and permitting. Glenn said Plant Prefab tin get its houses up successful astir fractional the clip of accepted construction.
About a twelvemonth agone the institution built a 270,000-square-foot automated mill successful Tejon Ranch, wherever it churns retired afloat modules and panelized components. Machines chopped lumber and way inferior pathways; nail guns link joists, studs and upwind wrap; different machines stroke successful insulation, each guided by a integer model. While this is happening, contractors tin commencement doing prep enactment connected site, alternatively than being slowed down by the much linear progression of accepted construction.

A crane sets 1 of Cassette’s modular homes into spot successful Joshua Tree.
(Cassette)
For occurrence zones, the institution tin tailor its designs to see cementitious cladding, metallic roofs, tempered solid and rooftop sprinkler systems, Glenn said. The institution built fire-resistant homes aft the Woolsey occurrence successful Malibu and the Tubbs occurrence successful Northern California.
“It’s a spot of a crisis-tunity,” noted Dafna Kaplan, main enforcement of Cassette Systems, a modular homebuilding institution she founded successful 2020. Originally she planned to make stackable multifamily buildings, but she pivoted to single-family lodging and ADUs successful 2024.
Cassette’s modular products, which they telephone Jollies, are long, constrictive structures ranging from 40-foot-long one-bedroom/one-baths to 60-foot-long, two-bedroom/two-baths. Designed by L.A.-based Oonagh Ryan Architects and built by aggregate California-based manufacturers, the units are wrapped successful lapped fiber-cement panels and rated for wildfire zones, Kaplan said. They travel equipped with windows connected some sides positive utilities, cabinetry and more. Base modules scope from $160,000 (40 foot) to $200,000 (60 foot), not including transportation and tract costs.
Kaplan said the institution has signed contracts with 2 customers successful the occurrence zones and is hoping to physique arsenic galore arsenic 50 units successful these areas wrong the year. Although its projects inactive necessitate operation tract inspections, its gathering permits person been preapproved by the state’s Housing and Community Development office, redeeming a batch of time. (This is simply a immense vantage of astir modular projects, peculiarly successful California, which is proactive astir performing approvals astatine modular factories.)

The ruins of Alyson Dutch’s rental impermanent house, which was destroyed successful the Palisades occurrence on with her main house. She plans to instal a Cassette modular location connected the tract and unrecorded successful it until her superior residence is rebuilt.
(Cassette)
Because Jollies apical retired astatine 870 quadrate feet, Kaplan expects astir fire-affected clients to usage them archetypal arsenic impermanent lodging and yet arsenic imperishable ADUs. Client Alyson Dutch is doing conscionable that connected a tract successful Malibu.
“This buys maine time,” said Dutch, who is inactive figuring retired however to rebuild her home. “Building anyplace is hard and time-consuming, and if I could person an instant lodging the reply is yes.”
One of the astir blase modular companies astir is Dvele, which has produced 275 modules successful the U.S. and Canada. The institution is readying to physique a mill successful Southern California focused connected occurrence rebuilding. Its homes, which tin beryllium customized by combining various-sized modules, scope from 1 to 4 bedrooms and are solar-powered, built to maximize thermal ratio and indoor aerial quality. The company, laminitis Kurt Goodjohn said, is serving middle-class residents with homes that tally astir $250 to $300 per quadrate foot, not including tract costs.